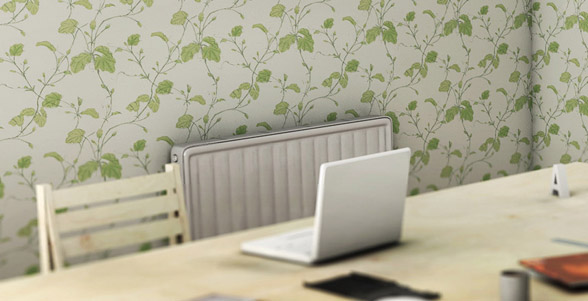
Monday 23 April 2012
The lightbulb conspiracy - Planned Obsolescence
The lightbulb conspiracy
Planned Obsolescence
At the beginning manufacturers will produce products that were long lasting, where overtime to support economic growth and wealth for business owners, engineers and manufacturer would decrease the lifespan of products.
Light bulbs were one of the first products that were affected by planned obsolescence. It is pretty contradicting of light bulb is one of our most intelligent invention even if there are light bulb that come last up to 100 000 hrs but it was never produced to the market. This whole planned obsolescence started taking it’s affect due to industrial evolution where machine made a lot of goods available. Consumers were not just buying what they needed but also what they wanted.
Where in 1929 when Wall Street crashed and people stop buying goods but everybody became to look for a job. Bernard London started the idea by law they introduced compulsory planned obsolescence, where all products has an expiry date (legally dead) and destroy, but it never took place.
On the other hand without planned obsolescence there wouldn’t be industries and designers, where it stated that designers should know how to design for business and how often the business wants consumers to repurchase their products.
Nylon stockings were pleased by consumers and the strength but to the point that engineers were forced to create fragile stockings. This causes frustration to old and new generation engineers and consumers.
Ipod were also a product that was affected a planned obsolescence but like when the battery died the company was not willing to change the battery. Apple would advise it’s consumers to change their ipods, where in the video people are fighting against planned obsolescence, due to the law case they now do longer warranties and battery replacement.
End of life of technology are dumped into developing countries and companies would say that they are second hand goods but they create environmental hazard. Where there are no more space to dump this waste on this planet and to adjust how companies are behaving when they are dealing with this waste.
As a designer planned obsolescence can be a bad thing that isn’t it upsetting that a product you design is not efficient and not life lasting, and my design was for a short period to satisfy people’s wants. Planned obsolescence do create jobs and keeping this world running but as a design I would need to think about where thing I design would be recycle and would not end up into third world countries. This video really have me inspired and showed me an inside of planned obsolescence.
Saturday 14 April 2012
Giving packaging a new life (2001, 7 episodes) and How it’s made: Packaging (2006, 6 episodes)
Giving packaging a new life (2001, 7 episodes)
• Recycling Paper – Paper 60% in use recycled material which is first sorted into different paper qualities, dissolved and pluper, the pluper then sorts out the impurities and print ink are removed. To achieve different paper qualities other raw materials will be add into the original paper texture that is settling on a paper machine. The paper will then be press, drained and dry, where then cardboard – paper will be produced into paper that can weigh up to 30 tonnes. These recycling paper will be the beginning of producing cardboard, in use in newspaper, tissue paper 70%
• Recycling Tetrapak (Beverage cartons)- Juice and milk cartons contain approx 80% cellulose (high grade paper fibres) which they are mix composites which includes cellulose, polypropylene which many contains use of aluminum. Water in the drum-pluper the recycled cartons swell and the plastic and aluminum separate from the cardboard. The recycled paper is then separate to produced premium quality paper. The other left over plastic and aluminum are then used in cement production plants. Composite cartons are sorted by infra-red light by “reflection” which they are sorted out into different categories by computer.
• Recycling Tinplate – Tin cans are sent to recycle factories where through magnets the tin cans are transported by machinery and compressed into metal blocks. Steel scraps produces about 40% usage of steel used in Germany( 15 000 steel slabs) , equally able to reproduce 9 billion new cans.
• Recycling Aluminum – separated by Eddie current separators (magnetic field acting in the opposite direction lift the trash off the belt and separates the aluminum) The sorted out aluminum waste would be sent to aluminum factories then reprocessed by melting, casted then roll. It can then be processed as aluminum sheets 1/20 of energy needed, which can be printed for new packaging. The left over waste from the process will go back to the production loop to be reprocessed.
• Recycling Glass – Glass with more than 10% of colour-ing needs to be separated before from clear glass recycling, which the glass are sent to plants for a secondary sort out into different glass recycling streams. Fragments which are smaller than 15mm are able to be sorted out into different groups even ceramic. The craps fragments are then scan by a electronic device, which the computer determines the impurities to be remove by accurate air jets that blows the pieces out. The prepare fragments are melted by soda, lime and sand before being shaped to be reprocessed into bottles again. Approx 2.7 million tones are recycled each year.
• Recycling Plastics - The boom of plastic packaging during the 90s, their end of life are usually incinerated (Burn) or landfill. Each year half a million tonnes of plastics are recycled each year more than 2/3 of the quantity that is produced. Plastics are sorted by automatic techniques into group – Bottles, Films, PET, Expanded Polystyrene (Foam) and “Mixed plastics” which are like plastic scraps. The plastics are then recycled into new products where expanded polystyrene are crushed and shaped into new product, old films are blow into new films in extruders, or plastics bottle turned into high grade regranulates. These granulates can be recycled into draining pipes, palates, sewage pipes, plants palates and children’s toys. Plastics are sorted by optical sort systems to increase efficiency, which these in-frared systems can clearly (accurately and reliably) separate polythene, polypropylene, polystyrene and PET. After the separation these plastics are “secondary raw materials” which are closer to pure raw plastics. E.g. PET in the separating drum the bottles are clean and aluminum parts remove by a magnet then the bottles are crushed into tiny pieces, a blower removes move of the label fragments, the polypropylene of the bottle caps are then separated by the “flow sink methods”, then the PET chips heated with soda lime are then heated in a rotary klin to remove any impurities and dirt. Dried and clean the PET are transferred to the ground stock sorting unit, where each grain are scan by a colour unit and blow out in a fraction of a second which can be reproduce into clear drinking bottles. Mixed plastic can be reproduced window frames, profiling from rail track edgings and long lasting plastic palates. Mixed plastics are broken down, sorted, and capped into small palates through a palatisor which is then used in plants to produce menthol, pig iron, etc
• Sorting Innovations - Dry mechanical techniques are used in a drying drum, air separating techniques blow out films, belt magnets to sort out cans, infrared sorts out composite packaging and PET bottles, wet mechanical sorts out the paper fractions in large washing drums and the rest are exclusive plastic, aluminum is shredded. Aluminum is removed by Eddie currents and other plastics are removed by systems of centrifuges. After drying polystyrene and polythene are melted directly into regranulates.
As a designer I realise the choice of material for packaging and the product itself is very important to the fact that recycling process of all materials has a lot of impact to society. Some materials such as plastic recycling still have room of improvement, where the process of recycling is actually a long process. It is useful to have a general knowledge of where the material will go towards their end of life, and the fraction of it being recycled.
How it’s made: Packaging (2006, 6 episodes)
Cardboard Boxes – Invented in 1870s, which cardboards are made like a sandwich of 2 piece of paper of a middle piece of the “flute” (wavy paper) = a corrugated board. Production starts of a roll of recycled paper the roll feeds into the machine called corrugators to produce a wavy pattern. The paper are pressed between 2 ridged rollers with hot steam this shapes the way of the flute, another roller applies glue to one side of the flute (glue: water and starch) this is now the one liner sheet. The other side are then rolled with glue and stuck on, for strength (The waves creates an air cushion strengthens the liner) purposes some cardboard box will have double liner 2 flutes and 3 liners or different thickness in the flute. Also recycle paper is more malleable than non- recycled paper. The cardboard sides are then trimmed, then the corrugated machine then cuts it up, up to 9 times depending to the boxes size. The cardboard are then separates into layers by flexible luminate tongs called “fingers”. The workers will then do a quality control check before printing. Then the boards will be stack between 25 -80 depending on the size of the boards and their thickness (8000 board/ hr). The board first goes through a trim that creates the handles and flaps (90 boxes/min). The cut offs will be sent back to the paper mills which it can be reuse up to 6 times. A folding machine will bend them, then applies cold glue to sections that will join the box, the next machine folds the glue section then the box is finished. The boxes will then be printed where the ink will be water basic ink. The printing press applies the colour to the board one colour at a time at 4 printing stages.
Packaging tubes – each tube is made with aluminum which is a size of a coin due to its light weight and malleable. After aluminum is put in a lubricant called zinc stearant, the contain spins so the powder is equally mixed, prepares the metal for stretching later on. They are then slide into another contain which distribution them down the machinery individually. The metal will then be feed into a forming press, which they will then be impact extruded. Where each slug will then move onto a die to form the exterior including the neck, at the same time a mandrill will create the interior which hardens the metal (150 slugs/ min). The next machine uses compress air aligns the tube, the necks of the tube are trimmed by 2 synchronised roller. The top of the neck is also trim to create smoothness, where the packaging remains sealed. With heat the metal is softens, where 2 layers of eproxy lacquer is spray within the interior. The exterior will then be rolled with a layer of enamel paint, to have resistance to solvents and sun damage. Grippers place the tubes on long pins move into a oven for 7mins for the paint to dry. The tubes are then moved to the printing machine where each tube has a complete turn against the printer. The tubes then go back to the oven for the ink to dry, where the polyester print remains flexible. The next machine screws on the plastic caps. A layer of latex is spray within the inside of the tube to prepare for the tubes to seal. A worker will check up on the quality of each tube for paint chips and etc, 1/ 500 tubes. Then a stick layer of paper is stuck on the open ends of the tube to avoid them for twisting during shipping. Each tube sells approx 12 cent.
Packaging Tetrapak – Protects food product refresh up to one year without refrigeration. Tetrapak consists of 3 layers; plastic, paper and foil, which is entirely made from recyclable materials. Plastic makes it leak proof. Printing – transfers one layer at a time using solvent free ink, can have up to 6 colours. The paper board is then feed into a lamination machine that will join it to the plastic and foil layers. At the same time a micro film aluminum foil into the laminator, a gas flame heats the paper board, roller rolls all layers together. Then cut into 4 lanes to produce a smaller roll, which the rollers are sent to a packer. The roll will then be put in a filling machine then the film is then sterilized. Seals the material to one tube, filled the tube with product then cut the tubes into individual packages and folded. It’s a light weight and recyclable packaging.
Aluminum cans – Light weight material and recyclable. Sheet of aluminum are feed into a machine then punched into the shapes then bends it into a cup. The left over’s are then sent back to the factory to be recycled. The cup is then slot into a drawing machine, then draw the can, which the whole process is lubricated avoid the metal to break. The edges are then trimmed, washed (6 stage acid -> neutral water 140 degrees) , dry, vanished (blue ring under the can), printed, vanished again to protect the ink, oven and hardens the can, the neck is then created, creates a curve on the edge, check each can and pulls out ones that don’t meet standards, ships to the drink company.
Glass bottles – Glass uses less energy than metal and plastics. Silicon ash 45%, soda sand 15% and limestone 10% are the main ingredient to make glass. Where soda melts the silicon and the limestone makes it stronger, it also contains recycle glass “Cullet”. The ingredient is put into a furnace melts everything into liquid state. It then create same cut offs of gobs and then its blow into its shape and size in a die.
Plastic bottles and jars – Lighter to carry and shatter resistant. PET mix with recycle PET <10%, melts into thick plastic, shoots into a mould, (Pre-form - Hardens instantly), Pre-forms into a oven to improve thickness then into a Reheat stretch blower, blows into a bottle form, control testing, compression test, test resistance to vacuum pressure, then sent to food suppliers. The recycle plastic use is not from use food plastic it is actually plastic scraps due to hygiene purposes.
It is important to know how packaging are produce to find out what would be the best option with the product we are trying to pack. The production is so important because different product would have different effects if it’s not the correct choice of material, e.g. soft drinks.
• Recycling Paper – Paper 60% in use recycled material which is first sorted into different paper qualities, dissolved and pluper, the pluper then sorts out the impurities and print ink are removed. To achieve different paper qualities other raw materials will be add into the original paper texture that is settling on a paper machine. The paper will then be press, drained and dry, where then cardboard – paper will be produced into paper that can weigh up to 30 tonnes. These recycling paper will be the beginning of producing cardboard, in use in newspaper, tissue paper 70%
• Recycling Tetrapak (Beverage cartons)- Juice and milk cartons contain approx 80% cellulose (high grade paper fibres) which they are mix composites which includes cellulose, polypropylene which many contains use of aluminum. Water in the drum-pluper the recycled cartons swell and the plastic and aluminum separate from the cardboard. The recycled paper is then separate to produced premium quality paper. The other left over plastic and aluminum are then used in cement production plants. Composite cartons are sorted by infra-red light by “reflection” which they are sorted out into different categories by computer.
• Recycling Tinplate – Tin cans are sent to recycle factories where through magnets the tin cans are transported by machinery and compressed into metal blocks. Steel scraps produces about 40% usage of steel used in Germany( 15 000 steel slabs) , equally able to reproduce 9 billion new cans.
• Recycling Aluminum – separated by Eddie current separators (magnetic field acting in the opposite direction lift the trash off the belt and separates the aluminum) The sorted out aluminum waste would be sent to aluminum factories then reprocessed by melting, casted then roll. It can then be processed as aluminum sheets 1/20 of energy needed, which can be printed for new packaging. The left over waste from the process will go back to the production loop to be reprocessed.
• Recycling Glass – Glass with more than 10% of colour-ing needs to be separated before from clear glass recycling, which the glass are sent to plants for a secondary sort out into different glass recycling streams. Fragments which are smaller than 15mm are able to be sorted out into different groups even ceramic. The craps fragments are then scan by a electronic device, which the computer determines the impurities to be remove by accurate air jets that blows the pieces out. The prepare fragments are melted by soda, lime and sand before being shaped to be reprocessed into bottles again. Approx 2.7 million tones are recycled each year.
• Recycling Plastics - The boom of plastic packaging during the 90s, their end of life are usually incinerated (Burn) or landfill. Each year half a million tonnes of plastics are recycled each year more than 2/3 of the quantity that is produced. Plastics are sorted by automatic techniques into group – Bottles, Films, PET, Expanded Polystyrene (Foam) and “Mixed plastics” which are like plastic scraps. The plastics are then recycled into new products where expanded polystyrene are crushed and shaped into new product, old films are blow into new films in extruders, or plastics bottle turned into high grade regranulates. These granulates can be recycled into draining pipes, palates, sewage pipes, plants palates and children’s toys. Plastics are sorted by optical sort systems to increase efficiency, which these in-frared systems can clearly (accurately and reliably) separate polythene, polypropylene, polystyrene and PET. After the separation these plastics are “secondary raw materials” which are closer to pure raw plastics. E.g. PET in the separating drum the bottles are clean and aluminum parts remove by a magnet then the bottles are crushed into tiny pieces, a blower removes move of the label fragments, the polypropylene of the bottle caps are then separated by the “flow sink methods”, then the PET chips heated with soda lime are then heated in a rotary klin to remove any impurities and dirt. Dried and clean the PET are transferred to the ground stock sorting unit, where each grain are scan by a colour unit and blow out in a fraction of a second which can be reproduce into clear drinking bottles. Mixed plastic can be reproduced window frames, profiling from rail track edgings and long lasting plastic palates. Mixed plastics are broken down, sorted, and capped into small palates through a palatisor which is then used in plants to produce menthol, pig iron, etc
• Sorting Innovations - Dry mechanical techniques are used in a drying drum, air separating techniques blow out films, belt magnets to sort out cans, infrared sorts out composite packaging and PET bottles, wet mechanical sorts out the paper fractions in large washing drums and the rest are exclusive plastic, aluminum is shredded. Aluminum is removed by Eddie currents and other plastics are removed by systems of centrifuges. After drying polystyrene and polythene are melted directly into regranulates.
As a designer I realise the choice of material for packaging and the product itself is very important to the fact that recycling process of all materials has a lot of impact to society. Some materials such as plastic recycling still have room of improvement, where the process of recycling is actually a long process. It is useful to have a general knowledge of where the material will go towards their end of life, and the fraction of it being recycled.
How it’s made: Packaging (2006, 6 episodes)
Cardboard Boxes – Invented in 1870s, which cardboards are made like a sandwich of 2 piece of paper of a middle piece of the “flute” (wavy paper) = a corrugated board. Production starts of a roll of recycled paper the roll feeds into the machine called corrugators to produce a wavy pattern. The paper are pressed between 2 ridged rollers with hot steam this shapes the way of the flute, another roller applies glue to one side of the flute (glue: water and starch) this is now the one liner sheet. The other side are then rolled with glue and stuck on, for strength (The waves creates an air cushion strengthens the liner) purposes some cardboard box will have double liner 2 flutes and 3 liners or different thickness in the flute. Also recycle paper is more malleable than non- recycled paper. The cardboard sides are then trimmed, then the corrugated machine then cuts it up, up to 9 times depending to the boxes size. The cardboard are then separates into layers by flexible luminate tongs called “fingers”. The workers will then do a quality control check before printing. Then the boards will be stack between 25 -80 depending on the size of the boards and their thickness (8000 board/ hr). The board first goes through a trim that creates the handles and flaps (90 boxes/min). The cut offs will be sent back to the paper mills which it can be reuse up to 6 times. A folding machine will bend them, then applies cold glue to sections that will join the box, the next machine folds the glue section then the box is finished. The boxes will then be printed where the ink will be water basic ink. The printing press applies the colour to the board one colour at a time at 4 printing stages.
Packaging tubes – each tube is made with aluminum which is a size of a coin due to its light weight and malleable. After aluminum is put in a lubricant called zinc stearant, the contain spins so the powder is equally mixed, prepares the metal for stretching later on. They are then slide into another contain which distribution them down the machinery individually. The metal will then be feed into a forming press, which they will then be impact extruded. Where each slug will then move onto a die to form the exterior including the neck, at the same time a mandrill will create the interior which hardens the metal (150 slugs/ min). The next machine uses compress air aligns the tube, the necks of the tube are trimmed by 2 synchronised roller. The top of the neck is also trim to create smoothness, where the packaging remains sealed. With heat the metal is softens, where 2 layers of eproxy lacquer is spray within the interior. The exterior will then be rolled with a layer of enamel paint, to have resistance to solvents and sun damage. Grippers place the tubes on long pins move into a oven for 7mins for the paint to dry. The tubes are then moved to the printing machine where each tube has a complete turn against the printer. The tubes then go back to the oven for the ink to dry, where the polyester print remains flexible. The next machine screws on the plastic caps. A layer of latex is spray within the inside of the tube to prepare for the tubes to seal. A worker will check up on the quality of each tube for paint chips and etc, 1/ 500 tubes. Then a stick layer of paper is stuck on the open ends of the tube to avoid them for twisting during shipping. Each tube sells approx 12 cent.
Packaging Tetrapak – Protects food product refresh up to one year without refrigeration. Tetrapak consists of 3 layers; plastic, paper and foil, which is entirely made from recyclable materials. Plastic makes it leak proof. Printing – transfers one layer at a time using solvent free ink, can have up to 6 colours. The paper board is then feed into a lamination machine that will join it to the plastic and foil layers. At the same time a micro film aluminum foil into the laminator, a gas flame heats the paper board, roller rolls all layers together. Then cut into 4 lanes to produce a smaller roll, which the rollers are sent to a packer. The roll will then be put in a filling machine then the film is then sterilized. Seals the material to one tube, filled the tube with product then cut the tubes into individual packages and folded. It’s a light weight and recyclable packaging.
Aluminum cans – Light weight material and recyclable. Sheet of aluminum are feed into a machine then punched into the shapes then bends it into a cup. The left over’s are then sent back to the factory to be recycled. The cup is then slot into a drawing machine, then draw the can, which the whole process is lubricated avoid the metal to break. The edges are then trimmed, washed (6 stage acid -> neutral water 140 degrees) , dry, vanished (blue ring under the can), printed, vanished again to protect the ink, oven and hardens the can, the neck is then created, creates a curve on the edge, check each can and pulls out ones that don’t meet standards, ships to the drink company.
Glass bottles – Glass uses less energy than metal and plastics. Silicon ash 45%, soda sand 15% and limestone 10% are the main ingredient to make glass. Where soda melts the silicon and the limestone makes it stronger, it also contains recycle glass “Cullet”. The ingredient is put into a furnace melts everything into liquid state. It then create same cut offs of gobs and then its blow into its shape and size in a die.
Plastic bottles and jars – Lighter to carry and shatter resistant. PET mix with recycle PET <10%, melts into thick plastic, shoots into a mould, (Pre-form - Hardens instantly), Pre-forms into a oven to improve thickness then into a Reheat stretch blower, blows into a bottle form, control testing, compression test, test resistance to vacuum pressure, then sent to food suppliers. The recycle plastic use is not from use food plastic it is actually plastic scraps due to hygiene purposes.
It is important to know how packaging are produce to find out what would be the best option with the product we are trying to pack. The production is so important because different product would have different effects if it’s not the correct choice of material, e.g. soft drinks.
Sunday 1 April 2012
Re- Post 11th Hour
The 11th Hour (2007)
The 11th Hour (2007)
Problem
People’s illusion that we are suffering from nature, but we are part of nature; and we are nature.
People may not realise that everything we do to improve civilization are causing danger to our ecosystem, and host “our planet”. Reports and solutions to “global warming”, “Greenhouse gas” and moving to other places are not just scientist trying to catch attention but series of abnormal nature behaviour. Such as tsunami, earthquakes, floods, drought, extreme temperatures etc can be all linked into messages nature are sending us.
Scientists want us to realise the way that we are treating our resources today, will one day run out. The consequence of these valuable resources at risk will cause risk to future civilization for human. The way that human’s superior attitude of living is killing themselves faster, than any other species on this planet.
People may not realise sickness such as asthma and allergies might be just the beginning of the affect of damaging the air and food qualities. Our next generation of children around 30%-60% in each classroom do have asthma, which it won’t be surprising if numbers are still increasing. Also the significant increasing number of different types of cancers, originating from the changing in our daily food and artificial chemicals unknowingly invades our lives.
In reality small amount of people in the world that has more power than the rest of the populations, to make economic decides, for their own financial benefits.
Such as Rich petrol companies are controlling our petrol prices
Where it’s time that nature has rights too, to have a say of how we are treating it. The way that how we are treating the planet are not going to give us sustainable growth, which defects the idea of economic growth and quality of live and contradicts an economist idea of “economic growth”. Technologies can never replace everything that nature can do, and can never do it the same.
The way to fix the wrong is “education” but at the moment our next generations are ignorant of what choices are made. As a designer we are the start of the consumer chain, and it’s really important we are educated correctly of how we treat our resources to sustain the beauty of our world. Where I believe every design and productions would need to be considered deeply of the harm we are doing to our motherland, because it is damaged enough. To out run politician and rich companies selfish decisions and as designers little changes we make, over time would make a difference to our planet and avoid extinction.
The 11th Hour (2007)
Problem
People’s illusion that we are suffering from nature, but we are part of nature; and we are nature.
People may not realise that everything we do to improve civilization are causing danger to our ecosystem, and host “our planet”. Reports and solutions to “global warming”, “Greenhouse gas” and moving to other places are not just scientist trying to catch attention but series of abnormal nature behaviour. Such as tsunami, earthquakes, floods, drought, extreme temperatures etc can be all linked into messages nature are sending us.
Scientists want us to realise the way that we are treating our resources today, will one day run out. The consequence of these valuable resources at risk will cause risk to future civilization for human. The way that human’s superior attitude of living is killing themselves faster, than any other species on this planet.
People may not realise sickness such as asthma and allergies might be just the beginning of the affect of damaging the air and food qualities. Our next generation of children around 30%-60% in each classroom do have asthma, which it won’t be surprising if numbers are still increasing. Also the significant increasing number of different types of cancers, originating from the changing in our daily food and artificial chemicals unknowingly invades our lives.
In reality small amount of people in the world that has more power than the rest of the populations, to make economic decides, for their own financial benefits.
Such as Rich petrol companies are controlling our petrol prices
Where it’s time that nature has rights too, to have a say of how we are treating it. The way that how we are treating the planet are not going to give us sustainable growth, which defects the idea of economic growth and quality of live and contradicts an economist idea of “economic growth”. Technologies can never replace everything that nature can do, and can never do it the same.
The way to fix the wrong is “education” but at the moment our next generations are ignorant of what choices are made. As a designer we are the start of the consumer chain, and it’s really important we are educated correctly of how we treat our resources to sustain the beauty of our world. Where I believe every design and productions would need to be considered deeply of the harm we are doing to our motherland, because it is damaged enough. To out run politician and rich companies selfish decisions and as designers little changes we make, over time would make a difference to our planet and avoid extinction.
Subscribe to:
Posts (Atom)